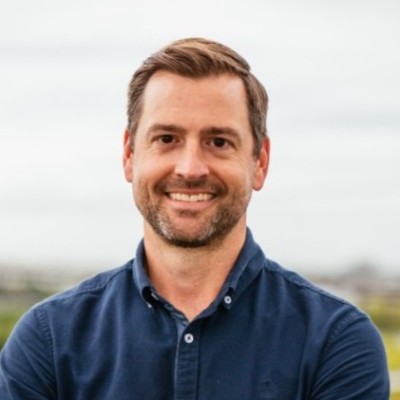
Adam Baker
During the height of the COVID-19 pandemic, supply chains were in crisis as ports around the world became overloaded. The Ports of Los Angeles and Long Beach famously had more than 100 cargo ships awaiting berth, reaching a high of 109 on January 9, 2022.
The congestion extended well beyond the ports as rail terminals also saw increased levels of congestion. This created additional challenges for companies that relied on the railroads to transport goods inland to distribution centers in central parts of the United States.
Due to this congestion, and increased dwell times at the ocean terminals, one top 100 US importer turned to transloading to get their products inland from West Coast ports faster.
What is Transloading?
Transloading is essentially transferring a shipment from one mode of transportation (e.g., ocean container) to another (e.g., 53’ trailer).
In this case, the company started taking its shipping containers from the ocean terminal to a warehouse facility near the port. The contents of each container are then transferred into 53' intermodal containers and dropped off at the rail terminal to be sent inland closer to their distribution centers.
For high-priority containers marked “hot”, the intermodal containers get loaded on a chassis and are trucked directly to the inland distribution centers for even faster receiving.
While transloading helped reduce receiving time by three to four weeks, it’s a more complicated and expensive process.
While Transloading Helped, Challenges Arose
Because their TMS didn't support integrating their drayage and transloading partners into their system, they initially started using an online project management software to try to manage everything. All partners in their transloading operations were brought into the system, including the drayage carriers, transload warehouses, and long-haul trucking companies.
The problem they ran into was that they were reliant on their transloading partners to manage the entire process and on the data their partners provided. Any time they thought there was an issue, they would have to go to the partner for any information they could get to try to understand the issue, and sometimes there wasn't much information to be provided.
In addition to external partners and the company’s logistics team, internal teams like the purchasing department and distribution centers also needed this information. The solution they initially chose became cumbersome with data fields that needed to be constantly updated manually by different parties. A lot of times the information wasn't accurate or up to date, and occasionally important data was missing.
Because of these struggles, they started looking for a tool that would give them visibility into their transloading and help them better manage the entire transload process themselves.
The Search for a Solution
With the new challenges the Company was facing with their transloading processes, they started looking for a transload software solution to help manage this part of the container lifecycle. This search led them to Gnosis Freight.
Gnosis’ engineering team began working with the company’s logistics team on some new supply chain execution tools for Drayage Scheduling and Transload Management. These CLM Enhancements were developed and added to their Container Lifecycle Management™ platform (“CLM platform”) to be used exclusively for the containers that would be transloaded. This amounted to approximately 80% of their West Coast import volume. These allocations were set up to run automatically by the CLM platform based on specific criteria provided by the Company.
The remaining 20% of the Company’s West Coast volume would still be tracked within the CLM platform, but their drayage would not be managed directly in it.
The Results
When asked, what have been the business implications of implementing Gnosis' Container Lifecycle Management platform and Transload Management and Drayage Scheduling tools?
"First, better execution. We're getting our product faster."
"Second, the visibility. We're not reliant on what our partners are saying, and we can go to them before a problem becomes a huge issue. We'll reach out to our partners about maybe 3 or 4 containers that are past their last free day at the port instead of our partners not telling us about 30 or 40 containers past their last free day."
Thanks to Gnosis Freight’s proprietary Marlo™ container tracking engine, most of the data that used to be entered manually is now updated automatically with complete and accurate data. This gives the company a new level of supply chain visibility they haven't had before.
Instead of relying on their partners to manage the process, they can proactively forecast import container volumes, and manage the associated drayage carriers and transloaders across their West Coast import locations.
"Gnosis has helped reduce demurrage and detention charges across the board, but most significantly on the transload side."
While some of the reductions in demurrage and detention charges can be attributed to congestion easing at West Coast ports, the 98% reduction in average demurrage fee, and 87% reduction in average detention fee on transload containers since implementing Gnosis is staggering.
Demurrage charges on transload containers dropped from an average of approximately $550 per container in June 2022, the first full month of Gnosis, to less than $12 per container in December 2022. Coming in lower than their non-transload containers.
At the same time, detention charges for transload containers dropped from an average of nearly $1,100 per container in June 2022 to less than $150 per container in December 2022. Again, below their non-transload containers, which have also come down significantly.
Overall, between June and December of 2022, the company saved approximately $6.5 million on transload related demurrage and detention alone!
.png)
"All the parties that we work with from a transload management standpoint are fully in Gnosis and it's exactly what we wanted. We're now digging further into Gnosis to see what else we can improve in our supply chain."
Schedule a demo if you’d like to learn more about the Container Lifecycle Management platform, Transload Management, or any of our other 20+ CLM Enhancements that can be tailored to fit your logistics needs.