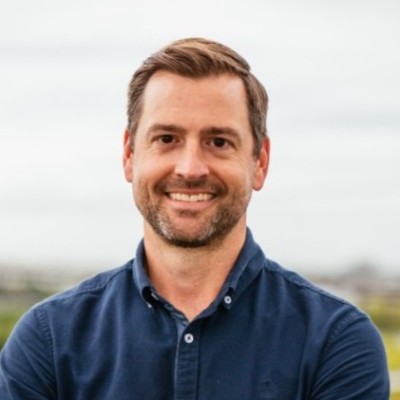
Adam Baker
Have you ever sat down and mapped out the downstream effects of your container tracking data quality and the software you use (or don’t use) to manage your containers?
There are a number of KPIs that can be directly impacted by a company’s ability to effectively track and manage their containers. We wrote about those here. The two that can have the biggest impact across a business’s operations are Container Dwell Time and Container Turnaround Time.
In case you aren’t familiar with these terms, container dwell time measures the amount of time a container spends waiting to be picked up from or returned to the port. Container turnaround time, on the other hand, measures the time it takes for a container to be unloaded, reloaded, and returned to the port empty or loaded with different goods for shipment.
At Gnosis Freight, we often talk about the importance of having container tracking data with a minimum of 98% completeness and accuracy, and the lowest possible latency when the container is approaching the terminal, but why is that so important?
For one, if it's any worse, your logistics team won't trust it and will go back to the old ways of checking carrier and terminal websites, ultimately wasting a lot of time.
More importantly, it can lead to inaccurate logistics and supply chain planning, that can negatively affect the business in a multitude of ways.
At Gnosis, our customer’s testing, and our own internal testing, has measured our data to be the most complete and accurate available when compared with other container tracking data options.
As for latency, the importance of latency varies depending on where the container is in its lifecycle. For example, when the container is in the middle of the ocean it may only be updated once per day, but as the container approaches the terminal, the need for lower latency data becomes increasingly important.
Due to the various data sources we utilize, and the way our data model is built, certain elements of our data are refreshed every 15 minutes, while others are less often, but in general the overall latency decreases (data is updated more frequently) as the timeliness of the data becomes more important through the container’s lifecycle.
But having better data doesn’t solve the problem if you don’t have a way to use the data – and to execute your processes effectively.
Like our CRO, Michael Rentz, likes to say, “People don’t want to see data, they want to use data.”
That’s where having the right software, like the Container Lifecycle Management® platform comes into play.
Having the highest quality data, and a software platform to execute on that data, has given our customers more control of their container logistics processes and helped them reduce their container dwell times and container turnaround times significantly. Here are a few examples.
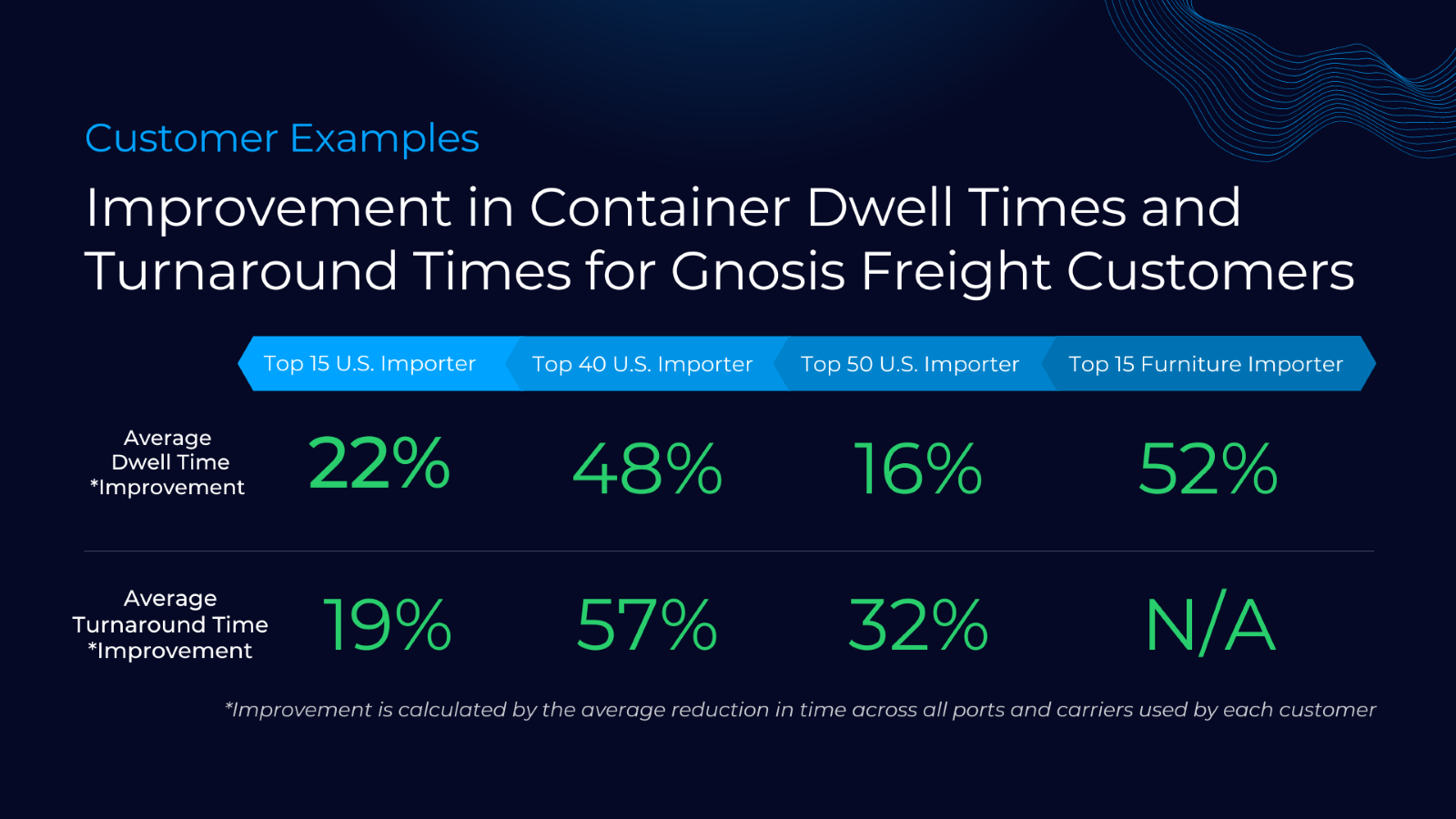
There are a number of factors that can contribute to a company’s dwell time and turnaround time, such as the number of last free days they receive on and off port as part of their ocean carrier contracts.
For example, one of the companies mentioned above gets upwards of 14 days of free time on port, but only 5 days of free time off port, which is the opposite of most companies’ contracts.
Regardless, being able to better control and improve these KPIs can have some significant downstream effects.
The Downstream Effects
What are some of those downstream effects?
The most obvious one that directly impacts the logistics team is a decrease in demurrage and detention, of which our customers see an average 85% reduction in the first three months.
The chart below shows the reduction in demurrage and detention charges for one of the companies mentioned above after switching to Gnosis from another leading visibility provider.
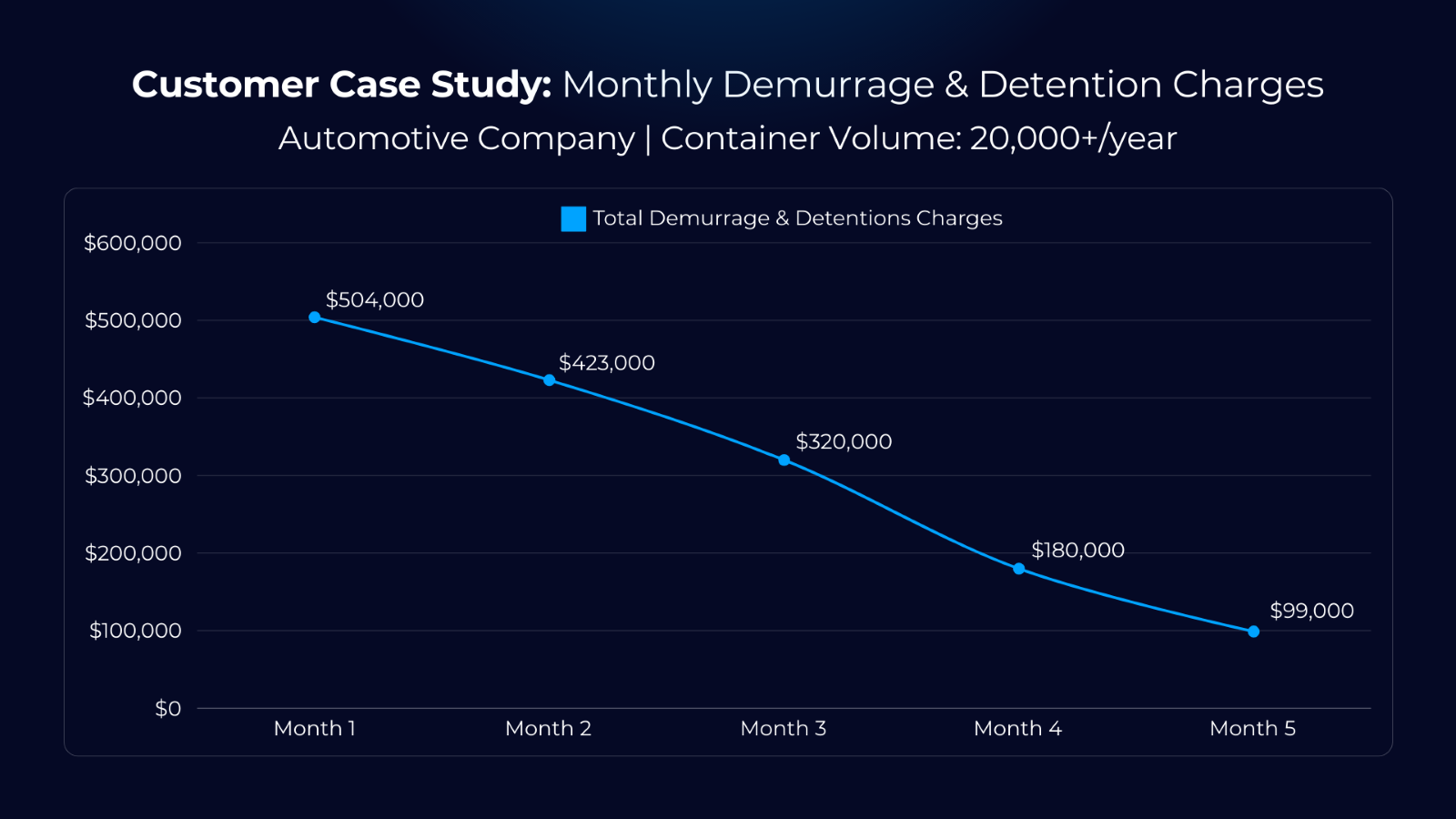
This is just one example; you can see more examples in our previous article How Last Free Day Milestones Help Save Millions on D&D.
While demurrage and detention are easy to attribute, other downstream effects can positively impact other departments throughout a company.
Here are some of the other areas that our customers have told me they’ve seen improvements in, thanks to the completeness and accuracy of our data.
- Shortened lead times between when an order is made and inventory is available for sale, which results in faster conversion of inventory to cash.
- Improved production line planning for manufacturers due to better knowledge of when raw materials and components will arrive at the plant.
- Improved warehouse labor scheduling to unload containers due to having better information well in advance about when a container will arrive at a DC to be unloaded.
- Faster and more accurate freight and per diem invoice auditing.
- Discounts from vendors for faster payments.
- Improved customer satisfaction due to having inventory on-hand and available for sale.
- Reduction in emissions associated with dry runs to the terminal to pick up containers that aren’t yet available.
- Improved employee satisfaction across departments leading to lower turnover.
I'm probably missing some others, but these are the ones I've heard about in my conversations with customers.
Have you experienced other improvements thanks to improved container dwell time and container turnaround times? If so, let me know.
Each of these above can be affected positively or negatively by container dwell times and container turnaround times, and ultimately impact revenue, expenses, and business risk.
The Container Lifecycle Management platform empowers logistics teams to do their job. But they don’t just manage exceptions, the downstream effects allow for the contribution to all aspects of the business. So, CLM isn’t just logistics software, it’s business software: empowering business through logistics.
It really is a smarter way to track and manage your containers.