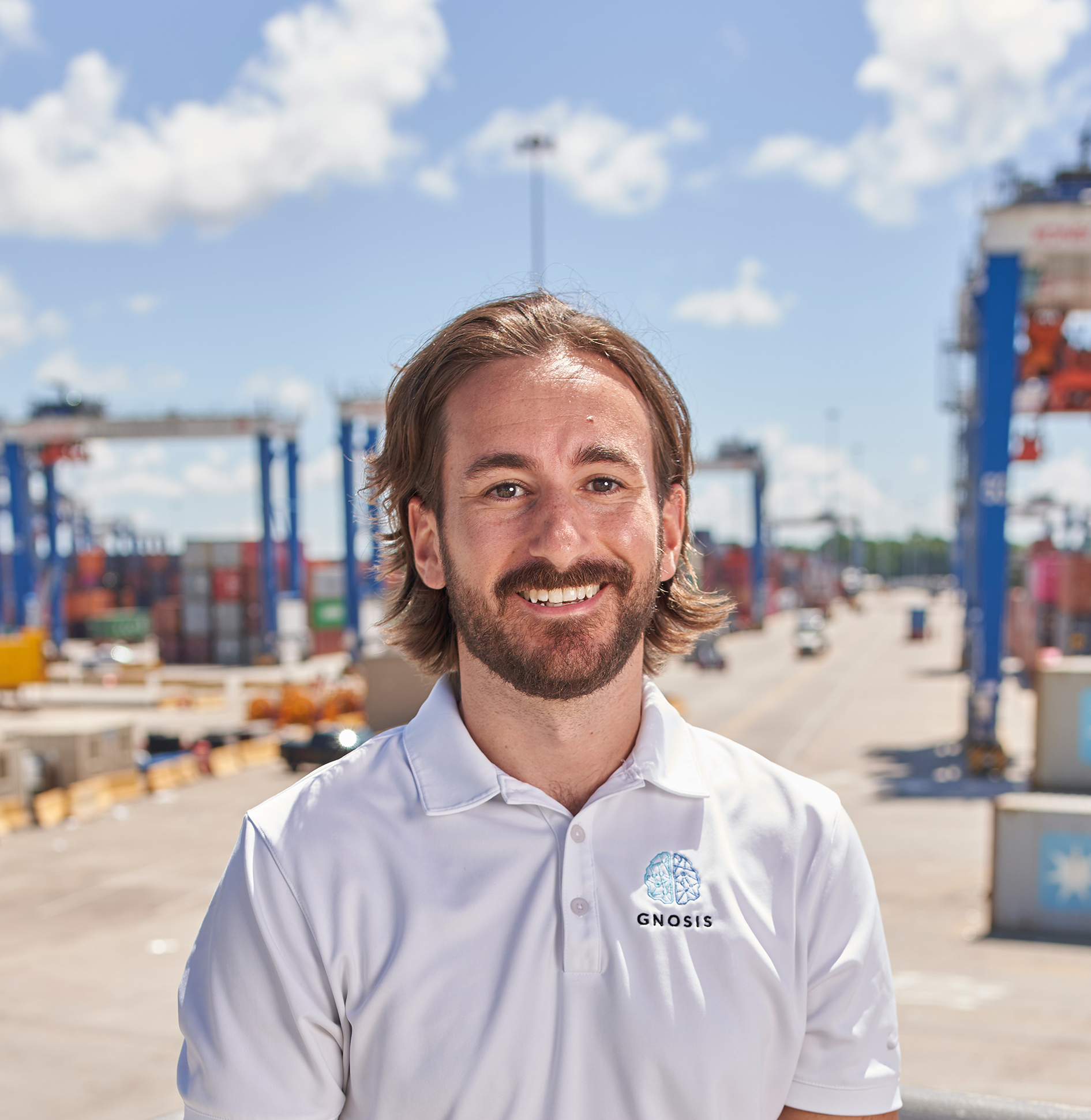
Michael Rentz
What is Container Lifecycle Management?
On average, a container changes hands 20 times during its journey. The common misconception is that "supply chain visibility”, which everyone defines slightly differently, solves the inherent supply chain and logistics problems we are all familiar with.
The question shouldn’t be, “Where is my container?”
The real questions are, “When is my container available to be transferred/picked up? Who are the responsible parties? And, are they doing their job appropriately and on time?”
For these reasons, the shipping container —and more specifically, the movement of the container — is conceptualized— and most importantly, managed — in lifecycles.
At the highest level, it could be broken down into three macro-lifecycles:
- Booking
- Tracking
- Scheduling
That is exactly how Gnosis is designed.
Within each of these macro-lifecycles live smaller, more granular, micro-lifecycles.
Booking, Tracking, and Scheduling happen in this specific order of the container's lifecycle. The difference with Gnosis, is we start our Product/Service with tracking. This is done because tracking is the most ubiquitous part of the supply chain — most companies do this part similarly. In contrast, booking and scheduling are unique to each company.
Booking takes place at origin, tracking takes place from "port to port" (ocean), and scheduling takes place from port to final destination. These apply to the container, not necessarily the goods inside of the container.
Within each of these macro-lifecycles, there are multiple micro-lifecycles:
Booking: PO management, cargo readiness, dispatch of equipment, stuffing the container, making the booking on the ocean carrier, getting the goods to the port, etc. The parties involved in this vary but are a unique collection of some of the following: BCOs ("Beneficial Cargo Owner"), Freight Forwarders, Ocean Carriers, Booking Agents, Origin Offices, and Factories.
Tracking: Where is the vessel, when will it arrive, US Customs, managing delays, when will it berth, when will the container be available for pick up. The parties involved in this are: The Ocean Carriers, Freight Forwarders, Ports, Terminals, US Customs, BCOs, and AIS GPS data.
Scheduling: Drayage, getting the container out of the port, getting it to the distribution center, getting the empty container back to the port. The parties involved in this are: The ports, terminals, trucking companies, yards, distribution centers, BCOs, Freight Forwarders.
Chronologically, the micro-lifecycles are:
Booking:
- Purchase Order cut
- Factory arranges goods and provides cargo ready date
- Booking arranged by booking party (NVOCC, VOCC, etc.)
- Confirmation of Booking
- Container dispatched from port
- Container is stuffed with goods
- Container is ready to be picked up
- Container is in-gated at port
Tracking:
- Container is loaded onto a vessel
- Vessel gives ETA
- Vessel sails across the ocean
- Vessel calls ports listed on string
- ISF (US Customs) filed
- Goods need to clear customs
- Vessel “arrives” (could be out in the ocean anchored or idling)
- Vessel receives a berth at the terminal
- Terminal starts to unload (“work”)the vessel
- Container is unloaded
- Container is available for pick up
Scheduling:
- Container is assigned to a destination
- Container is assigned to a drayage provider (trucker)
- Delivery Order is issued
- Trucker accepts the load
- DC appointment is issued (if applicable)
- Trucker picks up container
- Container “out gates”
- Container is trucked to DC
- Container arrives at DC
- Container is emptied
- Container is picked up by trucker
- Container is empty returned(“in-gated”)
(Note: These micro-lifecycles are for ocean freight tracking only. Rail container tracking and air freight tracking have their own separate micro-lifecycles.)
When managing the inbound flow of their containers, our customers (the BCO’s — think retailers) think about them in two dimensions:
- In what lifecycle is it?
- Is it moving or stuck (disrupted)?
Different lifecycles have different levels of importance, and typically, the closer it is to the final destination, the more important it is to make sure it isn't stuck somewhere on its journey. When you are moving a lot of volume (1,000+ containers per month), this is a burdensome process.
Some of the statuses that our customers think about with regards to dimension one listed above are:
- At Origin
- Loaded Vessel
- In transit on Ocean
- Arrived at the Port
- Available for Pickup
- Customs Cleared
- Out-gated from Port
- Delivered to DC
- Container Emptied
- Empty Picked Up
- Empty Container Returned
.png)
Each one of these statuses has potentially hundreds of containers in it. This is where dimension two comes into the picture. If some of these containers get "disrupted," different costs are incurred, depending on where they are in the lifecycle. And different lifecycle disruptions are more expensive than others.
Further, certain lifecycles update the likelihood that there will be a disruption downstream in a more expensive lifecycle. It is a giant puzzle that changes every second that is amplified by the total number of containers a company has moving.
Finally, these containers are not moved by one single party/carrier. They are typically moved by at least 5 different parties in any one lifecycle. BCO's diversify their risk across a handful of carriers to make sure if something bad happens, their containers (but really INVENTORY) aren't stuck somewhere. Adding it up all, there are 20 different parties that touch the container every journey.
Because of this, BCO’s have multiple different reports, in totally different formats, that they must manage between all the parties listed above, every single day…until Gnosis arrived.
Gnosis handles all these reports, usually sent as emails or excel files, automatically aggregating all the relevant information into one place in a standardized format, providing as close to real time visibility as possible. This allows our customers to quickly focus on the most expensive supply chain disruptions or highest priority containers.
This improved supply chain visibility takes Gnosis customers from spending 99% of their time just looking for the exceptions (disruptions) and only 1% trying to fix them, to 1% of their time looking for exceptions and 99% of their time fixing the issues. This change helps reduce costs and saves a significant amount of time each week. In some cases, saving millions of dollars per year.
This multi-dimensional lifecycle approach that Gnosis takes is exactly how our customers conceptualize their job and their supply chain processes. They are toggling through the macro-lifecycles, drilling down to the micro-lifecycles, looking for disruptions, planning additional capacity, labor, and equipment for the next lifecycle, evaluating costs, and keeping the containers moving. With Gnosis, they can do this with just a few clicks.
Want to learn more about how the Gnosis Container Lifecycle Management platform can help solve the challenges you’re facing with your supply chain?